Limescale formation on Critical Equipment in the field of :
- High / Medium / Low Frequency Induction Furnace
- Casting Industry
- Blow Molding
- Injection Molding
- Metal Injection / Gravity casting
- Plastic Manufacturing
- Forging Industry
Is detrimental to the Efficiency, Operation and Maintenance resulting in huge losses to these Industries.
Cooling in casting industry is an important process as it affects the production rate and the machine operating stability. Cooling is required in:
1.Induction heating on electric circuit (or coal fire)
2.Cooling for furnace body
Melting furnace utilizes induction furnace that melts the iron, stainless steel, or copper. The heated furnace is required to be cooled and avoid the high temperature on equipment. If the blockage of water pipe, by limescale interferes with cooling, this will harm the furnace. To effectively cool the equipment, the water quality is topmost priority.
Dangers of limescale in Manufacturing Industry
Good Quality Cooling water is the very important for most casting industry. It’s the reason that pure water is used as cooling liquid for the induction furnace.
Cooling system that utilizes Open Cooling Tower with plate heat exchanger have its pros and cons:
Advantages |
Disadvantages |
|
|
|
|
|
|
|
In long-term view, the stability of SPL closed circuit cooling tower is much higher than plate heat exchanger. Therefore, SPL would suggest to replace the Open type Cooling tower with the closed circuit cooling tower.
There are several advantages of SPL Closed Circuit Cooling Tower:
1.Increase in heat dissipation area, reduction in potential of limescale formation
2.Eliminates the need to regularly recharge water to prevent limescale concentration
3.Decreasing the shutdown situation caused by overheating
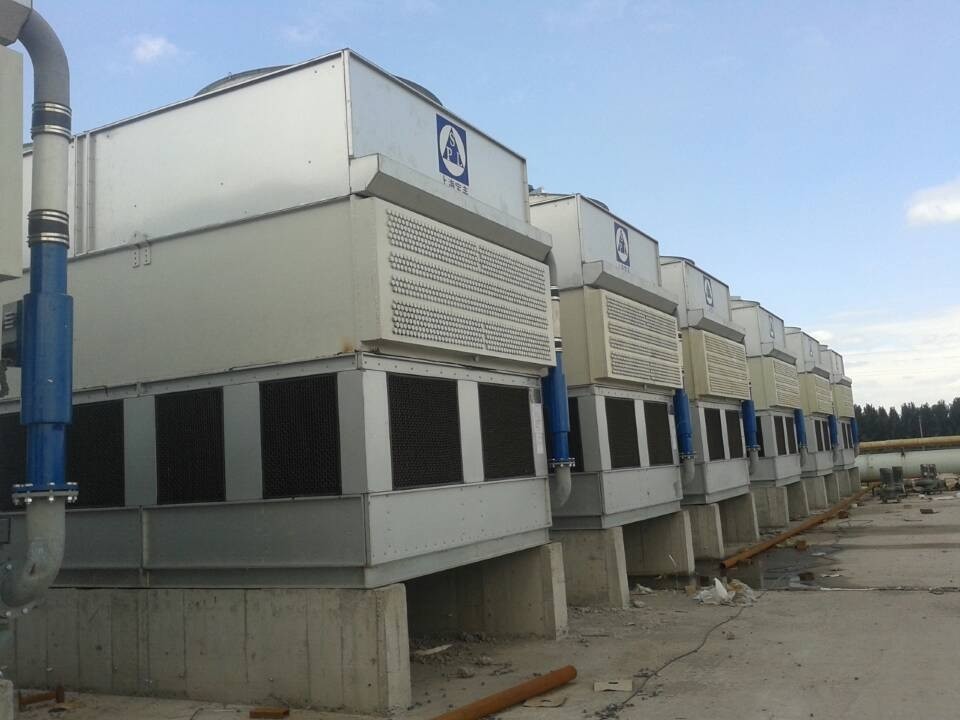
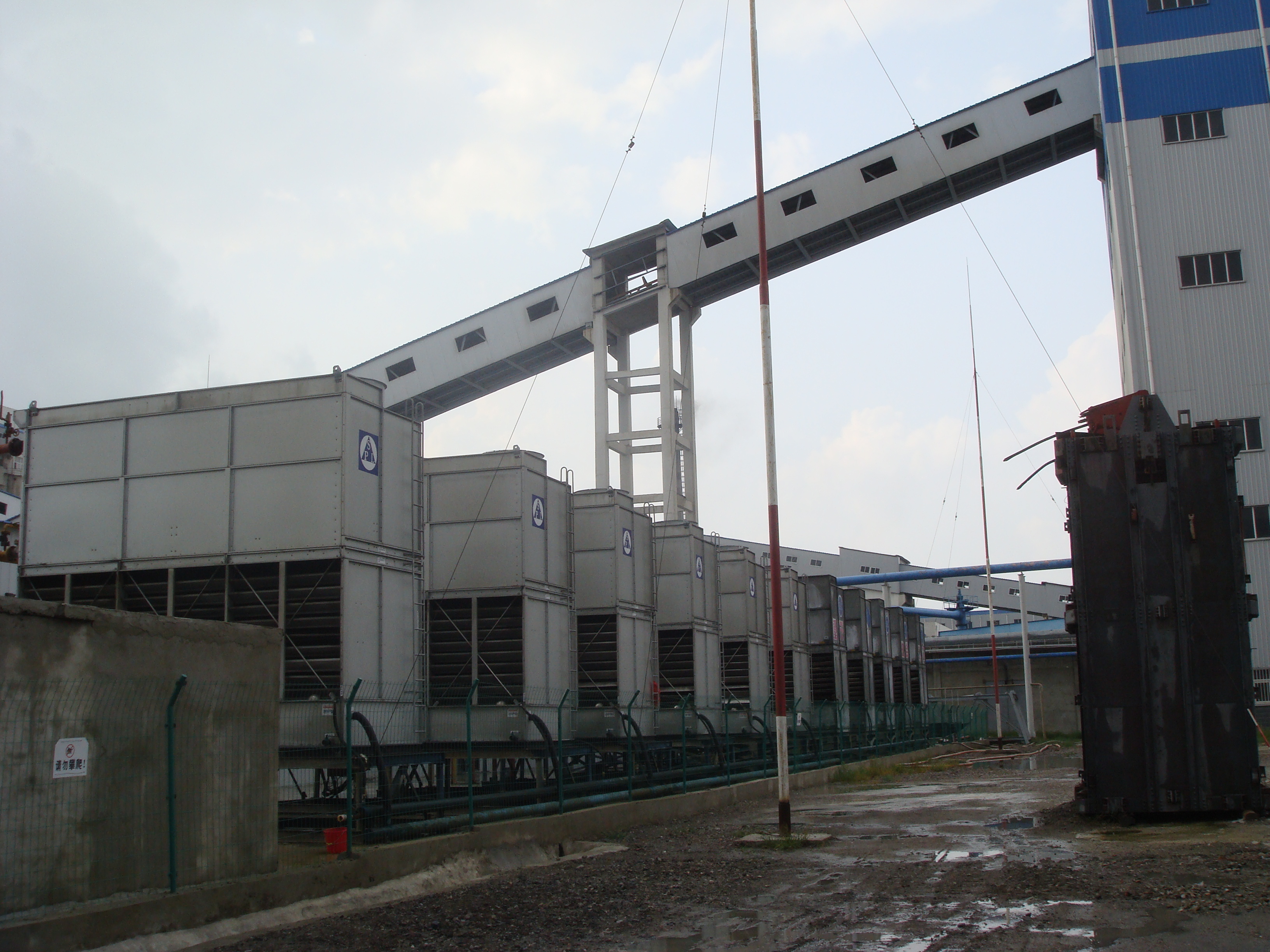
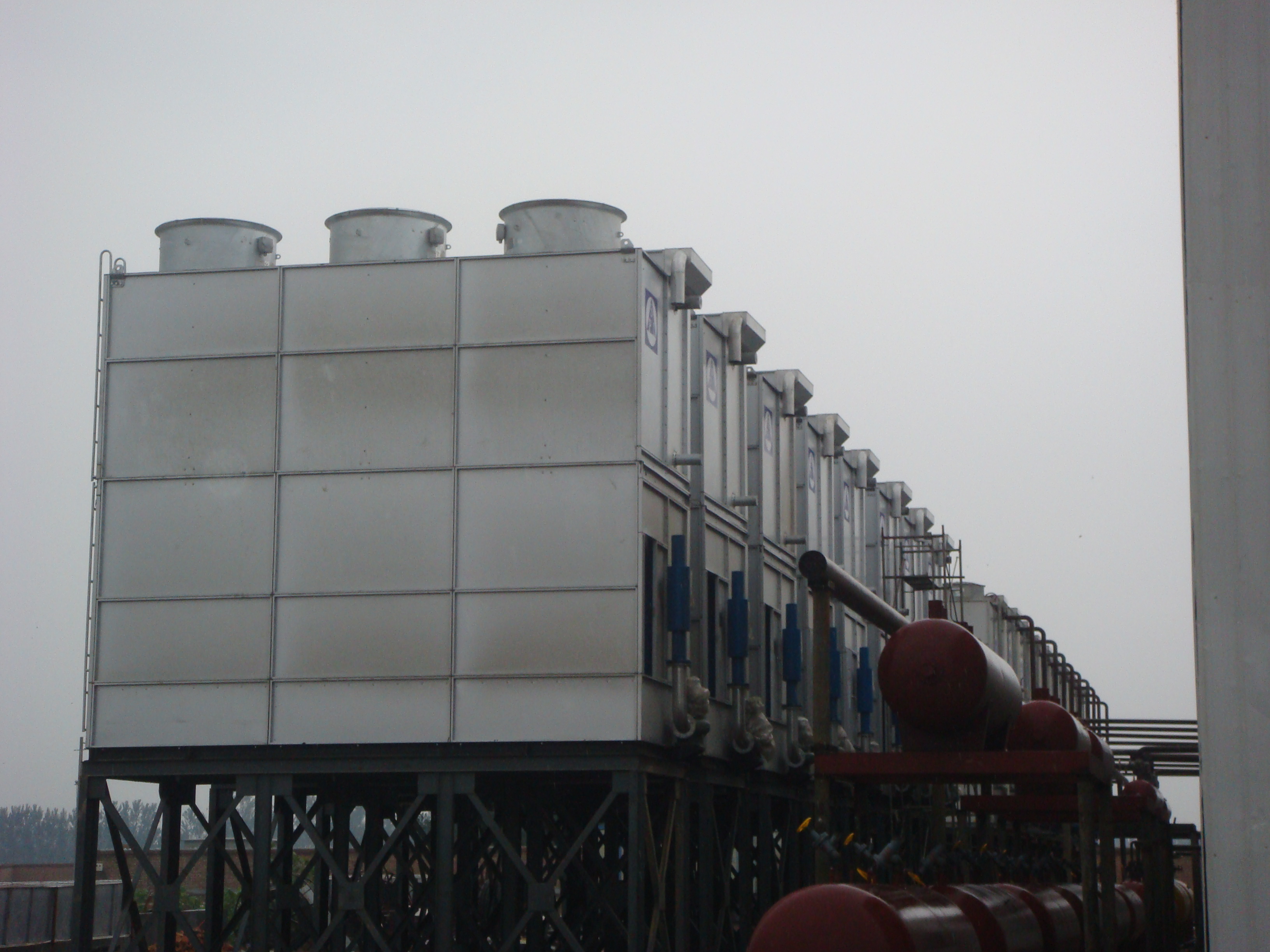
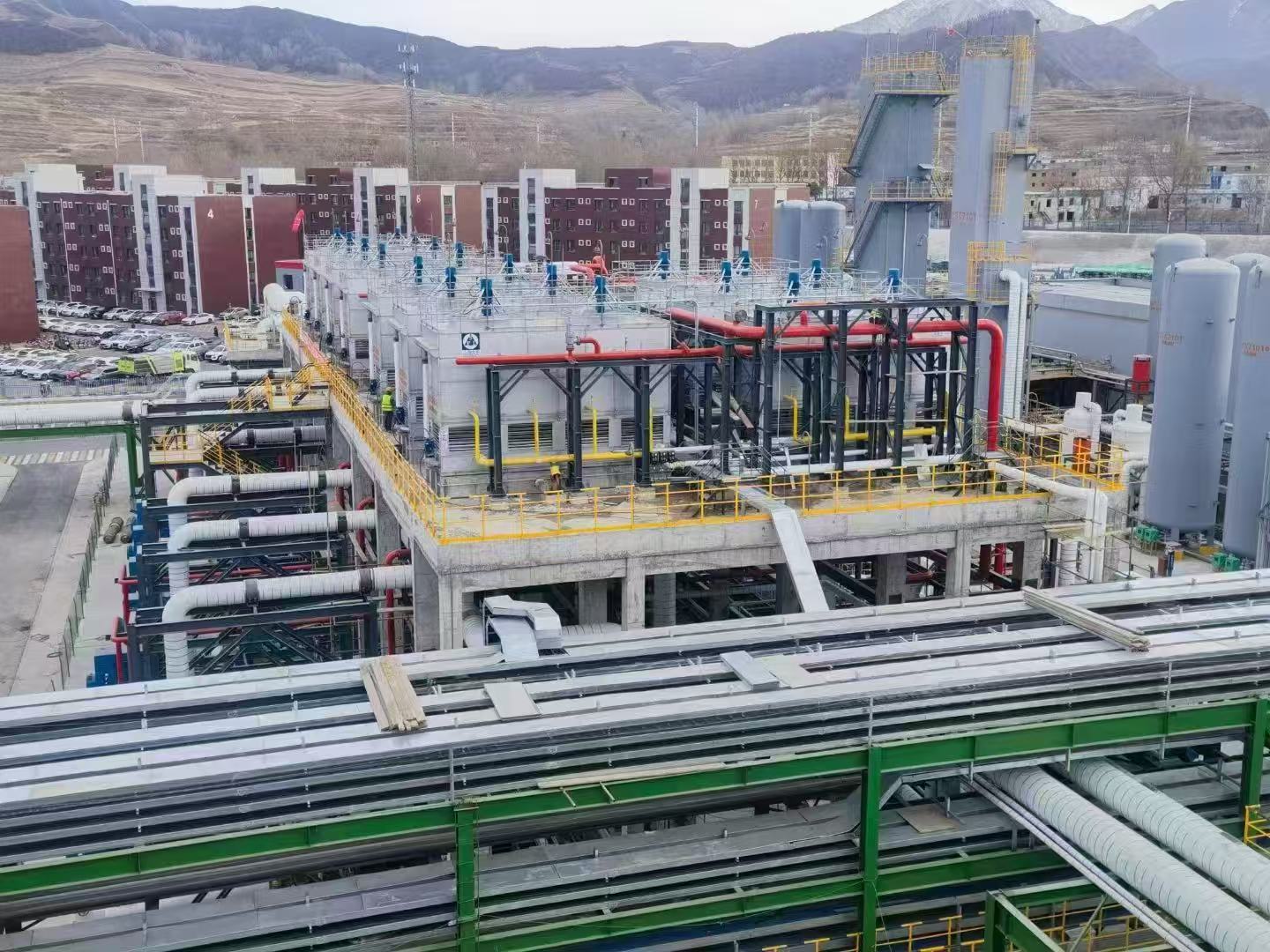
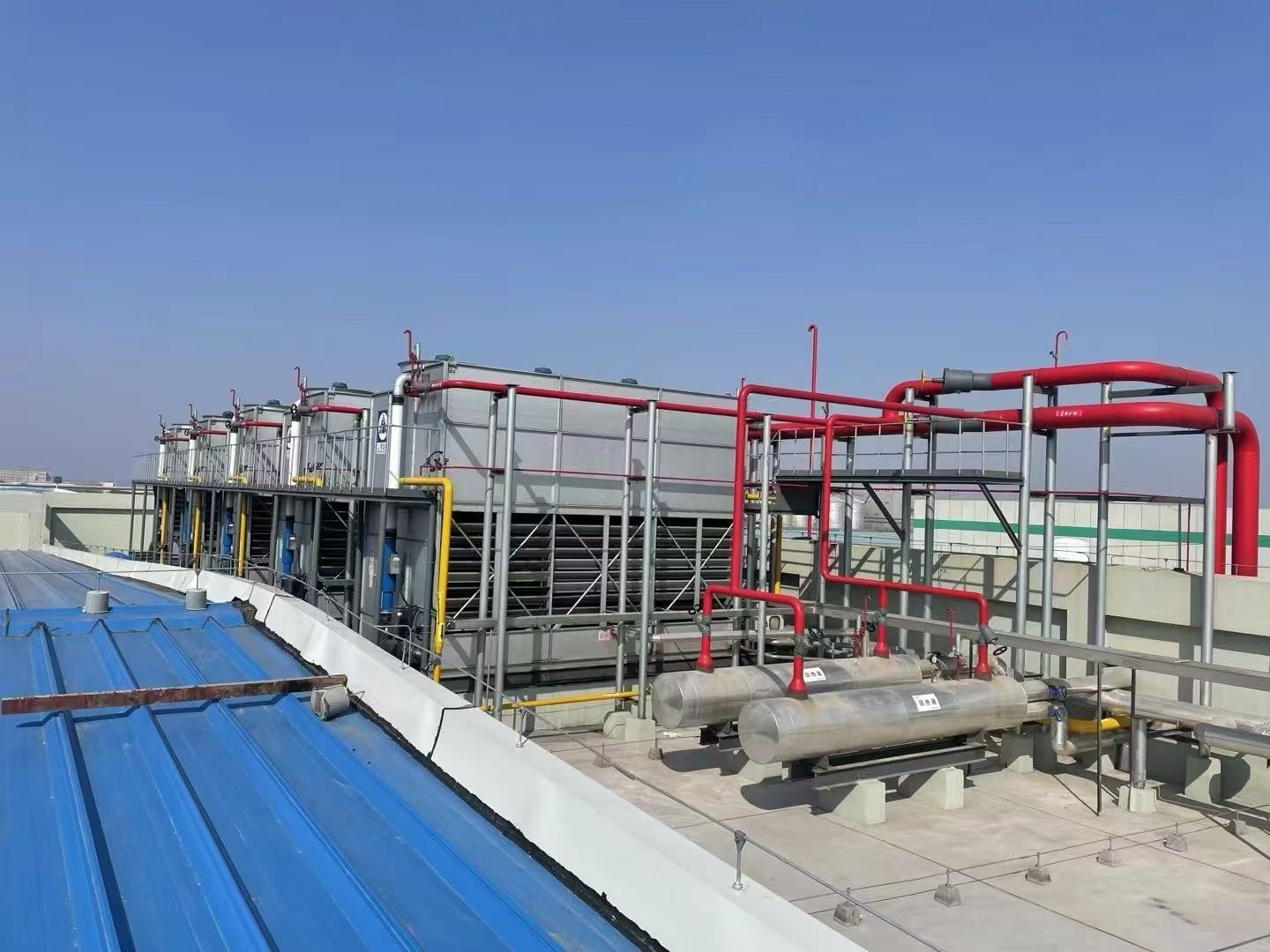
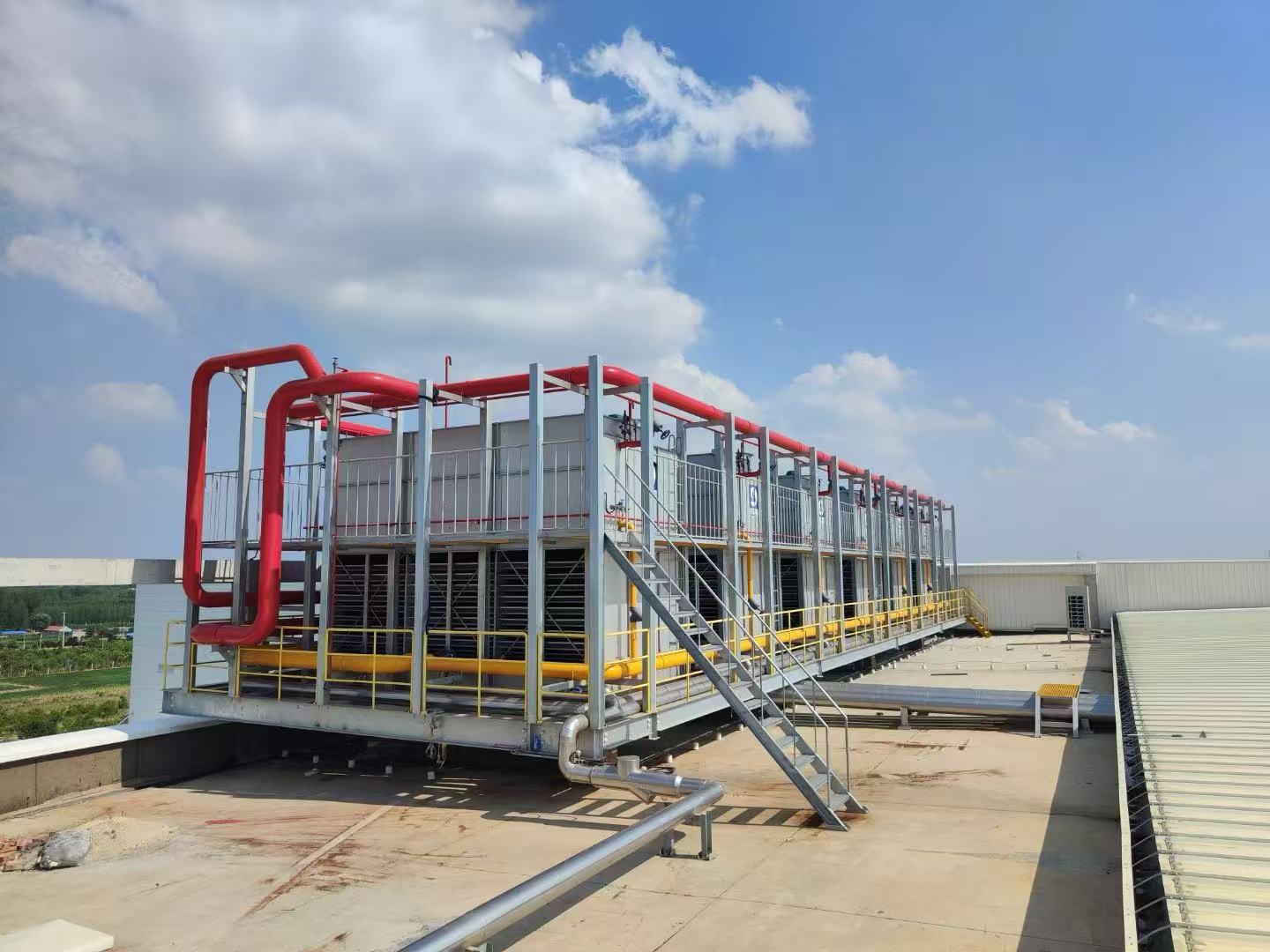